Tarkkuuskoneistuksen maailmassa ylivoimaisen laadun ja suorituskyvyn saavuttaminen on ensiarvoisen tärkeää. Yksi alue, joka vaatii erityistä huomiota yksityiskohtiin, on sylinterilohkojen valmistus, joka on kriittinen komponentti eri teollisuudenaloilla. Tämä artikkeli perehtyy räätälöidyn alumiinin tarkkuuskoneistuksen alueeseen, tutkien automaattisten sorvin viimeistelytekniikoiden käyttöä ja kovaanodisoinnin soveltamista pinnalle. Nämä edistyneet prosessit tarjoavat merkittäviä etuja, jotka takaavat paremman kestävyyden, paremman estetiikan ja paremman toiminnallisuuden sylinterilohkoille.
Räätälöity alumiinin tarkkuustyöstö sisältää monimutkaisten osien valmistuksen alumiiniseoksesta huolellisella tarkkuudella ja asiakkaan vaatimuksia noudattaen. Alumiini, joka tunnetaan kevyestä, korroosionkestävyydestä ja erinomaisista lämmönpoisto-ominaisuuksistaan, on suosittu materiaali monilla teollisuudenaloilla, mukaan lukien autoteollisuus, ilmailu ja elektroniikka.
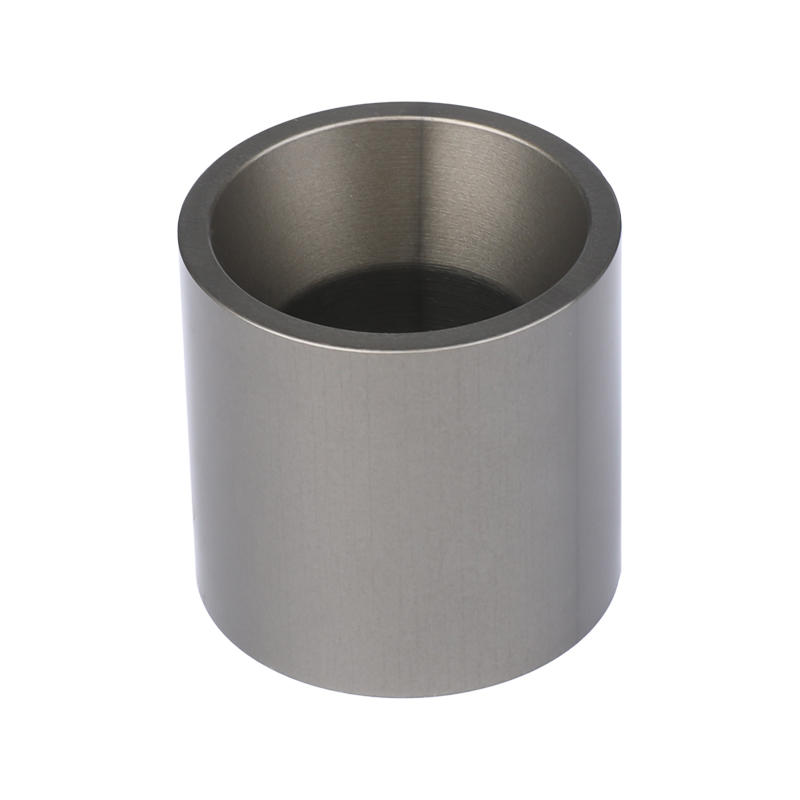
Automaattinen sorvin viimeistely:
Automaattinen sorviviimeistely on huippuluokan koneistustekniikka, jolla muotoillaan ja jalostetaan sylinterilohkoja poikkeuksellisen tarkasti ja tehokkaasti. Tämä automatisoitu prosessi käyttää tietokoneohjattuja sorveja, jotka on varustettu erittäin tarkoilla työkaluilla ja huippuluokan ohjelmistoilla monimutkaisten geometrioiden, porausten ja kierteiden tuottamiseksi. Automaattisen sorvin kyky työskennellä useilla akseleilla samanaikaisesti mahdollistaa nopeammat tuotantosyklit ja varmistaa tasaisen laadun koko valmistusprosessin ajan.
Käyttämällä automaattista sorviviimeistelyä valmistajat voivat saavuttaa tiukat toleranssit, tasaisen pinnan ja tarkan mittojen hallinnan. Tämä tarkkuus on ratkaisevan tärkeää sylinterilohkoille, sillä pienetkin poikkeamat voivat vaarantaa toimivuuden ja suorituskyvyn. Lisäksi tämän prosessin automatisoitu luonne minimoi inhimilliset virheet, lyhentää tuotantoaikaa ja optimoi resurssien käytön.
Kova anodisointi pinnalla:
Alumiinisylinterilohkojen kestävyyden ja toimivuuden parantamiseksi pintaan levitetään usein kovaa anodisointia. Anodisointi on sähkökemiallinen prosessi, joka muodostaa suojaavan oksidikerroksen alumiinin pinnalle parantaen korroosionkestävyyttä ja kovuutta. Kovaanodisointiin kuuluu alumiiniosan alistaminen tiukemmalle anodisointiprosessille, mikä johtaa paksumpaan ja tiheämpään oksidikerrokseen.
Kova anodisointiprosessi luo esteen sylinterilohkon ja ulkoisten elementtien, kuten kemikaalien, kosteuden ja hankaavien materiaalien, välille. Tämä suojakerros lisää merkittävästi kulutuskestävyyttä, pidentää komponentin käyttöikää ja parantaa sen kykyä kestää ankaria käyttöolosuhteita. Lisäksi kova-anodisointi voidaan räätälöidä tietyn pinnan viimeistelyyn, kuten mattapintaiseksi tai kiiltäväksi, mikä tarjoaa esteettistä vetovoimaa toiminnallisten etujen ohella.
Edut ja sovellukset:
Automaattisen sorvin viimeistelyn ja kovan anodisoinnin yhdistelmä alumiinisylinterilohkoissa tuottaa useita merkittäviä etuja:
Parannettu kestävyys: Automaattisen sorvin viimeistelyn avulla saavutettu tarkka koneistus varmistaa sylinterilohkojen optimaalisen istuvuuden ja toiminnan. Kova anodisointi lisää ylimääräisen suojakerroksen, mikä parantaa merkittävästi kulutuskestävyyttä, korroosiota ja lämpövaurioita.
Parempi estetiikka: Kova anodisointi mahdollistaa mukautettavan pinnan viimeistelyn, mikä parantaa sylinterilohkojen visuaalista houkuttelevuutta. Tämä on erityisen arvokasta aloilla, joilla estetiikalla on ratkaiseva rooli, kuten autoteollisuudessa ja kulutuselektroniikassa.
Parempi toiminnallisuus: Räätälöidyn tarkkuustyöstön avulla saavutettu mittatarkkuus varmistaa oikean kohdistuksen ja yhteensopivuuden muiden moottorin osien kanssa, mikä optimoi yleisen suorituskyvyn.
Räätälöidyn alumiinin tarkkuuskoneistuksen sovellukset automaattisella sorvin viimeistelyllä ja kovaanodisoinnilla ovat erilaisia ja kattavat eri toimialoja, kuten auto-, ilmailu-, meri- ja elektroniikkateollisuutta. Näillä edistyneillä prosesseilla valmistetuille sylinterilohkoille löytyy käyttöä moottoreissa, hydraulijärjestelmissä, kompressoreissa ja monissa muissa mekaanisissa järjestelmissä.